Equipment Failure
Preventing Extensive Downtime
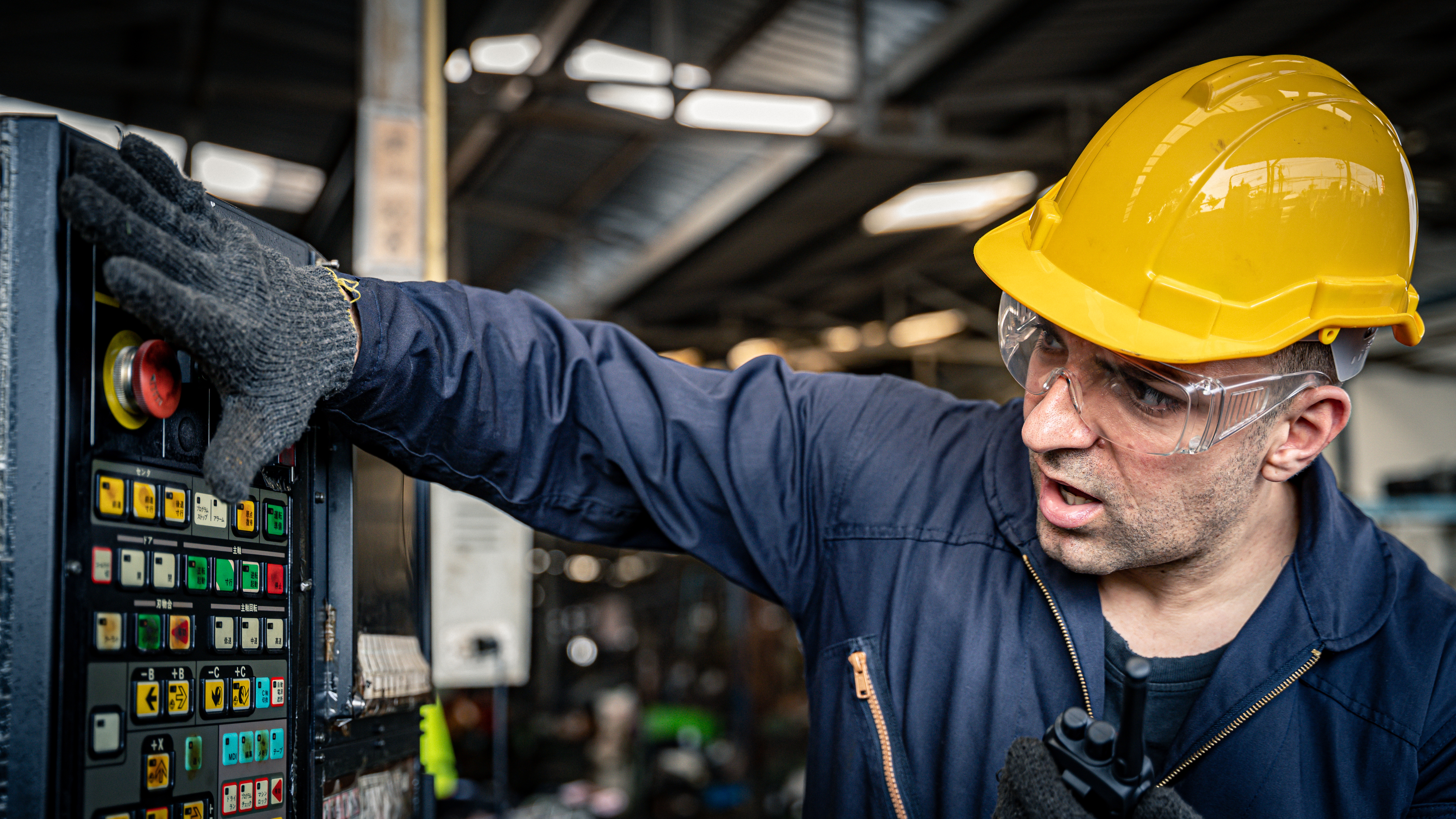
Equipment Failure
Accidental events and equipment failures in manufacturing industries can occur for many reasons, like the lack of knowledge and training, maintenance, reliability, or work methodologies. Equipment failure although unwelcomed is unavoidable and effects the entire production process. Fortunately, thanks to Industry 4.0 technology advancements, it’s become easier to predict and address the areas where failure is more likely to occur. Before worst-case scenario results occur, smart manufacturing technologies directly identify the areas that need maintenance or aren’t performing at their full capabilities.
Common causes of equipment failure are corrosion, threaded fasteners loosening, misalignments, and abrasive wear. Corrosion is an inevitable result of manufacturing because of weather and temperature exposure. Although there are coatings available to help prevent damage, harsh conditions and chemicals decrease equipment reliability and longevity. Whether it’s the consistent vibrations, shocks or torqueing, threaded fasteners will loosen. Even though threadlockers are applied regularly to help maintain the torque and clamp load, outside forces can cause bolts to loosen on a wide range of equipment. Since abrasive wear can happen anywhere and at any time when exposed to chemicals, extreme weather conditions, and intense pressure, equipment can become worn and reduce the equipment’s life. To address this, many manufacturers repair the surface wear and rebuild the worn areas to extend the equipment’s life. Alignment issues, on the other hand, often result from irregular vibrations or shocks. If bolts are loose then this throws alignment out of configuration. To address the issue, a threadlocker is applied to secure mounting bolts in place to prevent misalignment from reoccurring and maintain clamp load.
Industry 4.0 Technologies
Its without a doubt that equipment failures generate results that are less than desirable. They include all equipment and tooling failures, breakdowns, and any unplanned maintenance. On a smart manufacturing platform, the SHOPGRID® digital platform for example, automation and monitoring controls are implemented so machines can monitor and repair themselves, for the most part. To do so, the machines dynamically adjust manufacturing operations and conditions to ensure maximum efficiency is performed at all time.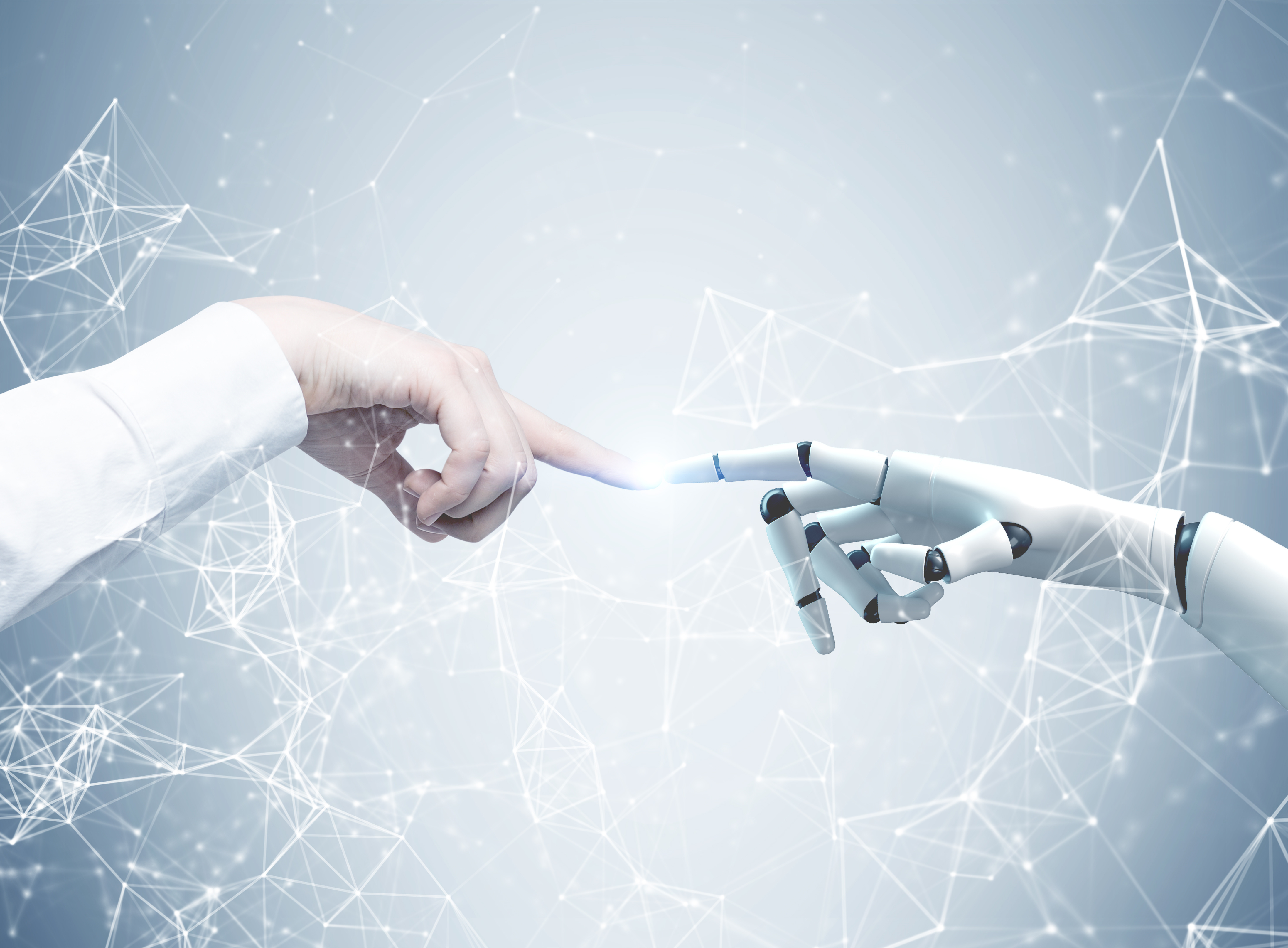
In today’s world, information is abundant and easily accessible with the right platform. By utilizing an Industry 4.0 compliant platform, it has never been easier to collect, analyze, and share data as it occurs in real-time from the shop floor. Gaining maximum visibility to all operational equipment and processes make every investment dollar count and provide tremendous feedback back to manufacturers seeking to make immediate improvements. SHOPGRID®’s digital platform is Industry 4.0 compliant and provides all operators the ability to customize and prioritize notification, alert, and display preferences. In addition, it monitors all machine maintenance, automated and operator-assisted, to know when, where, how, and why an action occurred. All recorded activity provides manufacturers the information they need to know how to improve operations, whether it’s from machine downtime or bottlenecks, the interference factored in when operators and engineers are the head of addressing maintenance at the source, and the accuracy percent they compare when reviewing production reports month to month.
Being one-hundred percent truly productive is the goal all manufacturers have. They want to be as productive as possible because that is how they make their money, please their customers, and stay competitive. By integrating and using Industry 4.0 technologies to monitor, control, and run operations makes a significant influence that cannot be surpassed by human labor. Automation, streamlining, and optimization has influenced the manufacturing industry for the better and has helped manufacturers reach and exceed their operational goals within the first year of integration.
No floor is too small for SHOPGRID®
Let's Automate Your Business Together!